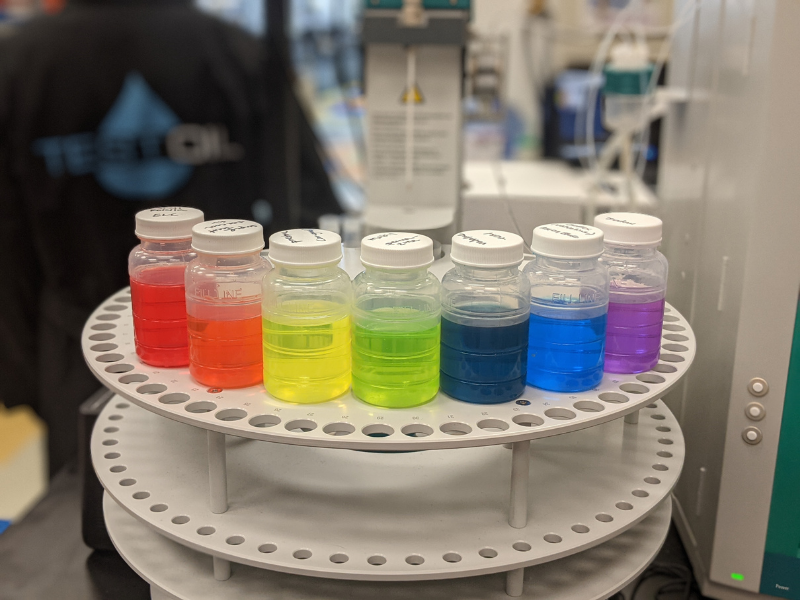
COOLANT TESTING
Every single year, up to 50% of all engine failures result from cooling system problems. Mineral deposits just 1/16th of an inch in size on 1 inch of cast iron are enough to decrease heat dissipation by 40%.
Avoid unscheduled downtime and control coolant consumption and disposal costs.
Conventional and extended life coolants both require testing to ensure the fluid can meet the demands of today’s heavy-duty diesel engines. Analysis of the coolant is essential to achieve optimum machine performance and engine longevity. Allow analysis experts to take the guesswork out of servicing this system through testing that promotes predictive maintenance programs. In-service coolant testing will increase uptime, decrease unscheduled downtime, establish proper drain intervals, and increase engine and fluid lifespan.
Eurofins TestOil offers two test packages to meet the analysis requirements of conventional and extended life coolants through standard analysis and comprehensive analysis, the standard test slate and advanced comprehensive test slate.
COOLANT TESTING METHODS
Eurofins TestOil offers two test packages to meet the analysis requirements of conventional and extended life coolants through standard analysis and comprehensive analysis, the standard test slate and advanced comprehensive test slate.
The Coolant Standard test slate delivers same-day results and benefits include the ability to determine when to extend drain intervals, avoid failures, improve the fluid condition, reduce component failure/downtime, and improve lifecycle management. This package is appropriate for conventional coolants.
The Coolant Advanced Comprehensive test slate includes all Coolant Standard test methods plus IC (Ion Chromatography), HPLC (High-Pressure Liquid Chromatography), and SCA Number (supplemental coolant additives). Benefits include all that the Coolant Standard offers in addition to a comprehensive look at extended life coolant additives.
The final comprehensive report delivers a clear picture of the coolant in the following five sections:
- Fluid Condition: Glycol concentration shows whether the right mix ratio is being employed. When lower than expected there is likely inadequate protection for the cooling system and engine. When higher than expected there will be a loss of heat transfer capabilities. Freeze and boiling points are dependent on glycol percent and are an indicator of the expected operating temperature range.
- Observations (Visual Analysis): Color, clarity, and foam provide an overview of the physical appearance of the coolant–any change will indicate likely degradation and/or contamination. Odors are checked for signs of contamination due to adverse conditions within the cooling system. Particles can appear for a number of reasons including a poor source of water, corrosion, cavitation, or defective electrical grounds.
- Contamination: An increase in conductivity indicates contamination originating from the water supply, such as hardness and fluoride, or combustion gases; sudden changes may be the result of overdosing inhibitor or concentrate or mixing with another coolant.
- Degradation: Glycolate indicates the primary breakdown of the glycol portion of the coolant which is generally caused by localized overheating or an air leak (i.e., combustion blow-by) within the system.
- Inorganic Additives: The presence and concentration of additives should be compared to the new fluid reference.
- Organic Acid Technology: The presence and concentration of these additives will appear in some Extended Life Coolants and should be compared to the new fluid reference.
- Wear: Wear metals are most commonly signs of corrosion or cavitation. They may also appear due to grounding faults, localized hot spots, or a poor water source.
Request More Information
For more information on Coolant Testing please complete the form below.